top of page
RESOURCES
Support Services
Instructions
Pull Down & Data Acquisition Support Services.pdf
Customer Bearing Spacer Form.pdf
Hub Bearing Spacer Instructions.pdf
Precision Bearing Packer Instructions.pdf
Alignment System Ordering Form.pdf
Data Acquisition System Ordering Form.pdf
DSS System Ordering Form.pdf
Technical Articles

Hub End Play Chart
GM Caliper Mount Jig Instructions.pdf
Dual Axis Caster/Camber Gauge Instructions.pdf
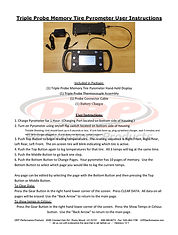
Triple Probe Memory Tire Pyrometer Instructions.pdf
Suspension Analysis Downloads
DRP DSS System Comparison.pdf
DRP Performance Equipment Terms.pdf
DSS Report Sample.pdf
Videos
DSS & Alignment Systems
DSS & Alignment Systems


Top 3 Reasons to Buy a DRP Pull Down System
00:28
Play Video

Get Fast, Faster with DRP Set Up Tools & Equipment
01:46
Play Video

DSS 4 Updated Start-Up Procedure
08:15
Play Video
DRP University Tutorials
DRP University Tutorials


What is DRP University?
01:10
Play Video

Our Greatest Product..!
01:40
Play Video

DRP DSS-3 Pull Down System.wmv
03:29
Play Video
bottom of page